Meet our People- Liza O'Kane, Quality Manager
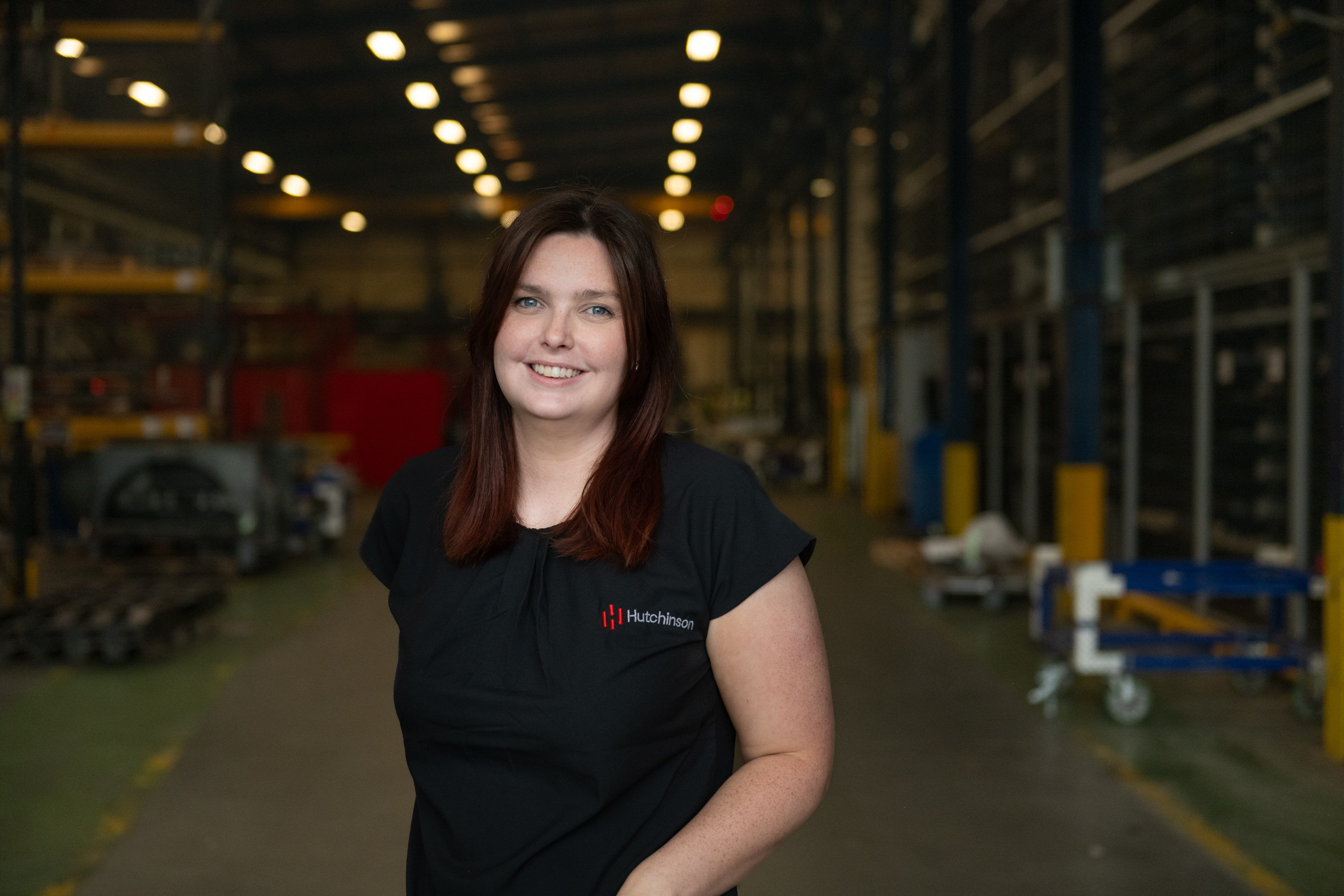
At Hutchinson, quality is at the heart of everything we do.
That’s why we’re excited to introduce one of the newest additions to our team-Liza O’Kane, our new Quality Manager.
With a background in mechanical and manufacturing engineering and a passion for continuous improvement, she’s already making an impact.
We sat down with Liza to learn more about what drives her, both on and off the job.
1. What’s your background, and what brought you into quality management?
I grew up in an Agi background so was constantly around machinery, which led me to study Mechanical and Manufacturing Engineering. That’s where I first picked up my understanding of quality processes. I actually got into quality management somewhat unexpectedly. I had a quality-related role early in my career and quickly discovered how much I enjoyed it. The mix of problem-solving, continuous improvement, and working across different departments really clicked with me. Since then, I’ve grown passionate about quality and take pride in helping teams deliver better products and processes.
2. What do you enjoy doing outside of work?
Outside of work, I spend most of my time with my kids and down at our caravan in Benone.
3. What does “quality” mean to you when it comes to the parts we deliver to customers?
To me, 'quality' means delivering parts that consistently meet or exceed customer expectations in terms of performance, reliability, and compliance with specifications. Ultimately, quality is about building long-term trust and reputation by getting it right the first time and continuously looking for ways to improve. The biggest indicator for me that our quality is good is that our customers keep returning and ordering more.
4. What systems or processes do we have in place to make sure every part meets spec?
We have several systems and processes in place to ensure every part meets specification. It starts with clear and controlled documentation, including up-to-date drawings and SOPs. During production, we use in-process inspections and first-off checks to catch any deviations early. We also carry out final inspections before parts are sent to the customer. On top of that, we conduct regular audits and monitor non-conformance trends to drive continuous improvement. All of this is supported by our quality management system, which ensures traceability and accountability throughout the process.
5. What’s one thing you’re focusing on right now to improve our quality even further?
Right now, I’m focusing on improving how we capture and respond to quality data on the shop floor and from customers. By strengthening our feedback loops-from inspection results to corrective actions-we can react faster to issues and prevent recurrence. I'm also working on enhancing our root cause analysis process, to ensure we’re not just fixing problems, but truly understanding and eliminating their sources. It’s all about driving a more proactive and data-driven quality culture.
We’re proud to have Liza on board as part of our commitment to building a strong, customer-focused quality culture. With her drive and expertise, we know our quality systems, and our customer relationships, are in good hands.
Welcome to the team, Liza!
Share this article
Latest Articles